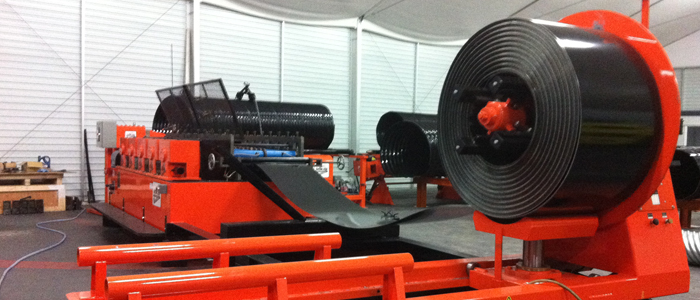
Corporate Profile: Ironside Design Manufacturing
Canada’s Ironside Design Manufacturing (IDM), the world’s leading manufacturer of Corrugated Steel Pipe (CSP) roll forming mills, has to date sold more than 150 of its machines around the world. This century old, Chilliwack-based corporation has a storied history of growth and success that began in British Columbia, then spread throughout North America and, finally, around the world. Their story is of great significance and relevance to all sectors served by the CSP industry, domestically and globally, which is why it is being profiled in “In The Trenches.”
The Early Years
In 1914, Scottish born George Ironside arrived in Chilliwack, B.C. from South Africa and took over the blacksmith shop started by the Stewart and Chadsey families. George successfully ran this shop for nearly four decades. During that time, the company had steadily built its reputation among local communities as an honest and trustworthy business.
The company name was changed to Ironside Machine & Welding in 1958 and was popularly known by its acronym, I.M.W. Then, in 2006, four years after splitting off from a separate division that manufactured natural gas compressors, the roll form division became a distinct corporate entity and was renamed Ironside Design Manufacturing Inc.
2014 marks the 100th anniversary of George Ironside’s introduction to the company as well as the beginning of a century of exceptional stability and growth for the company.
In the early 1950s, after having successfully run the company for nearly four decades, George Ironside was succeeded by his son, Bill, who continued to build upon his father’s legacy, expanding the business and bringing Herb Carrell on board in 1958 as an equal Partner.
In 1964, Bill sold his half of the company to Jim Nyssen, a recent Ironside addition who had demonstrated great leadership skills. Around this time, the seeds of a relationship between Ironside and the CSP industry were first sown and would quickly come to a fruition of mutual opportunity.
Helical Lock-Seam Pipe Machines: The Industry Game Changer
Under Nyssen’s tutelage and leadership, Ironside entered the CSP market in the late 1960s, leveraging his creation of one of the world’s first helical lock-seam pipe manufacturing machines – a creative and revolutionary piece of machinery, for which Ironside was soon receiving worldwide attention – and orders.
According to Shane Setter, Ironside’s Director of Roll Form Sales & Marketing, “Jim developed the new machine on the fly, and actually first drew it in chalk on the concrete floor of the plant to explain the concept. In fact, prior to making roll form machinery, we were a general blacksmith shop,” he says, “so we made many things.”
“But the primary machinery the company had been making prior to this time was a very simplified, one-pass mill for manufacturing panels used on the sides of campers. These machines simply added a few corrugations to strengthen the panels, which were madefrom very light gauge materials. The panels were then glued onto the sides of wooden campers. So, the introduction of the helical lock-seam pipe machines was a giant leap, in terms of mechanical complexity, from those earlier, simple panel mills,” he adds.
Soon, the company’s new machines were being shipped to destinations throughout the globe. And the advanced features of its helical lock-seam pipe machines established Ironside as the industry’s leading supplier of a complete manufacturing system for producing CSP.
Back then, riveted pipe had long been very popular as a primary type of pipe, as steel was then only available in sheets. Consequently, Nyssen received a request to build a roll former to form sheets for riveted pipe, rather than the conventional method of using a brake press. But, shortly thereafter, the Japanese began exporting steel in rolls, rather than sheets. So, Nyssen came up with the idea of a machine that could roll form coils of steel. That initiative is what led Ironside into metal forming.
A Chance Meeting of Complementary Minds
“How Jim Nyssen came to join the company is quite a story,” says Setter. “It all started with a serendipitous meeting. Nyssen had come to Chilliwack from Princeton, where had immigrated from the Netherlands in 1958, in response to a job offer. When he arrived however, the job fell through. A few weeks later, in a chance meeting at a service station, he connected with Herb Carrell,. At the time, Herb was desperate to hire a welder and mentioned it to the station attendant, whom he knew well.
“The attendant jokingly suggested to Herb that he hire Jim, a stranger neither had ever met before. And wouldn’t you know it, when Herb approached and asked Jim if he ever welded, against all odds, Jim responded yes, he was indeed a fully qualified welder, and even had his pressure welding ticket.
“The two hit it off immediately and Herb asked Jim to come and work for him. Jim said sure, since he was between jobs he’d be happy to work for Herb for a couple of weeks. But Herb clarified that he wanted Jim to come and work for him that very day, which he did,” says Setter, “so, in retrospect, it was quite a fateful chance meeting for them both.”
Nyssen was a natural businessman, an inventive thinker and a true innovator. And, after having purchased half the company from Ironside in 1964, just five years later, he owned it all. And it was while designing a roll form mill for riveted pipe, used on pot-bellied stoves, that he first started pondering the idea of replacing rivets with lock seams.
“Basically, Jim took the locking idea from stove pipes and combined it with the work he was doing in developing a machine to manufacture riveted pipe,” explains Setter, “That was the first step toward development of his first helical lock-seam pipe machine, which was the forerunner of the machines that are in use around the world today,” he adds.
They Built It, But No One Came… Well, Not at First
Although Nyssen had succeeded in building the machine, there were no orders, as people had trouble believing that it really worked. Undaunted, Nyssen started using his machine to build and sell pipe, as proof that the pipe it produced was of exceptional quality. Then, in 1969, Nyssen built and delivered two more mills – one of which was shipped to Prince George and the other to Nanaimo. At this point in time, Ironside was manufacturing pipe mills and selling pipe, as well.
“It was at this point,” explains Setter, “that both Nyssen’s invention and his company began to receive massive attention from around the globe. And I mean massive,” he adds. “Jim would call and invite as many people as possible to come and see what his machines could do,” says Setter, “and it worked in spades. By the 1970s and ‘80s the company was focused entirely on building roll forming mills and was shipping as many as 15 machines annually.”
The Introduction of Ironside Mobile CSP Mills
In 1983, Ironside launched the first portable version of its pipe mill, which had been under development for several years. Portability offered the tremendous advantage of manufacturing pipe on site, which, in addition to being convenient, also promised significant savings on shipping and other logistical costs. This first Ironside portable unit was built for an American government project to manufacture and install underground silos for guided missiles. However, that project fell through and the machine was instead shipped to Australia, where it remains in operation today.
“That first iteration of a portable mill was really just a stationary mill mounted on a flatbed,” explains Setter, “and there were some safety concerns regarding its stability, due to the excessive height of the machine,” he adds. “However, the next generation of portable corrugated pipe mill was not developed until 2004, when Ironside introduced the Mini Prowler, which was truly portable,” says Setter.
Ironside developed and built the Mini Prowler in partnership with Contech, a very large, U.S.-based corrugated steel pipe manufacturer. Using some innovative engineering, the machine was specifically developed to be as lightweight and portable as possible and included many new and advanced features vs. previous designs.
In 2009, with some clever engineering, Ironside pushed the envelope for improving portable pipe mill technology, yet again, with the introduction of its newest portable machine, the IDM Super-Capacity Mobile Pipe Mill. Being able to simply drive this new CSP mill to even the most remote job sites, plus its low working height and fast setup/breakdown time, were features that offered more adaptability and value to the end-user than ever before, which, of course, gave them a significant competitive advantage.
Featuring ground level height, a state-of-the-art touch screen command centre and a user-friendly wireless remote controller, the Super-Capacity mill even enables the operator to move around the machine while still in full control of its functionality and allowing the end user to manufacture pipe up to six metres in diameter. Up until the availability of the Super Capacity mill, this diameter was unheard of. To date, Ironside has sold and delivered IDM Super-Capacity Mobile Pipe Mills to customers in Canada, Australia and China, and is currently involved in negotiations with other international customers.
“Our current mobile mill is much safer, and enables operators to make better pipe for less money. It features a fully customized trailer that actually folds in on itself,” explains Setter, “so when it’s in transport mode, it can be modified to comply with 48-foot, 53-foot, or whatever maximum trailer length is specified in local D.O.T. regulations. Plus, it runs standard coil width – a huge advantage – and is able to handle virtually any profile, including bigger corrugations.”
Future Markets for CSP Mills
Today, throughout international markets, including Europe, Russia and China, opportunities are opening up very quickly for CSP products.
“Take China, for instance,” says Setter. “Until the beginning of this year, CSP was not permitted to be used on roads there; but, at the beginning of 2014, the Chinese government officially approved CSP for use in road construction. Being such an enormous country, with tremendous needs for maintenance, infrastructure and other projects ideally suited to CSP, China will continue to offer tremendous development potential, for many years to come,” he adds.
“The real key to our success as a company over the past century has always been our dedication to quality, supplying reliable machinery and our service,” he says. “It is a commitment that started with George Ironside and, today, we still believe the services and products we offer are second to none. We’re constantly searching for new and better ways to make our products faster, cleaner (greener) and more versatile,” he adds. “Our people are deeply committed to continued innovation and improvement, and our executives have intentionally held the reigns on the company’s growth, which is why, despite the tremendous worldwide success we’ve had over so many years, we are still a company of less than 40 people.”
“Rather than hiring and firing people to match transitory workloads, we have maintained a talented and tremendously experienced staff, most of whom have been with us for the long term,” explains Setter. “At Ironside, we’re very community oriented; here, collaboration and service excellence are not just buzzwords for a brochure; they are completely and genuinely ingrained throughout our staff and the entire company culture,” he says.
Elmer Niezen, President of Ironside summarizes the company’s past and future: “Notwithstanding our global accomplishments with Jim Nyssen at the helm, Ironside’s local business continues to remain equally important, because Jim never forgot where he got his original opportunity,” says Niezen.” We were honoured to have been awarded the Chilliwack Chamber of Commerce Business Excellence Award for Manufacturing, in 2008 and again in 2011,” he adds, “and despite a century of success, we’re still going strong and, frankly, the future’s never been brighter.”