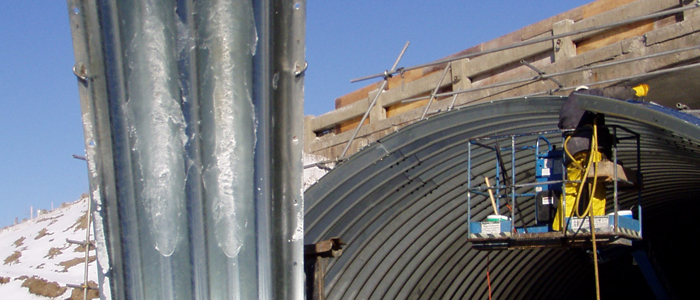
Canada’s First Installation of a Polymer Coated Deep Corrugated Buried Steel Structure Leads to Product Improvements
A Ministry of Transportation for Ontario (MTO) 2005 initiative to reconfigure Highway 401 through Kingston included replacement of an aging concrete bridge, which had protected a now-defunct road-over-rail underpass. The thoroughfare had since been adopted as part of a popular recreational trail used by local hikers, cyclists and cross-country skiers. Regardless of the replacement method chosen for this project, it was imperative that all lanes of Canada’s busiest highway, running directly above, be kept open during construction.
Although installation costs to install a concrete arch or steel plate structure would have been virtually the same, the cost to manufacture a new concrete structure would have been nearly twice that of a CSP plate solution.
The Birth of Polymer Coated Corrugated Structural Plate
Aecon, the general contractor on the job, had originally received a quotation from Armtec to replace the structure with the specified Galvanized Deep Corrugated Structural Plate Arch. At that time, however, Armtec had just commenced manufacturing a new variant of its Structural Plate and Deep Corrugated Structural Plate Bridges and Culverts, featuring polymer coated plates. This innovative coating system promised significantly longer service life in aggressive environments, due to the specific protective properties offered by the coating. Since Highway 401 is the primary road link between Windsor and Montreal, its heavy traffic counts and frequent applications of road salt during winter inevitably create high salt conditions on the roadway shoulders – an ideal location in which to test the new polymer product.
Armtec, through Aecon, approached the customer, MTO Eastern Region, to suggest they consider the alternative, longer term solution offered by the new polymer coated plate.
“At more than 60 metres in length, this steel arch was quite a sizeable installation, beneath one of Canada’s busiest stretches of highway,” explains Doug Lowry, (Senior Business Development Engineer, Armtec), “so it’s certainly not the kind of replacement job a customer would want to be doing again any time soon.”
In addition to the threat from a potentially high saline environment below the road, the option to erect the new structure inside the old one would leave little room for final cover on top of the new structure (1.2 to 1.8 metres, across its 11 metre span); that led Armtec to approach the MTO regarding consideration of its new, polymer coated product.
“Although they seemed genuinely interested,” says Lowry, “they were understandably reluctant to spend additional funds for a premium product which, at the time, had little history behind it. In the end, however, they did opt to coat a portion of the new structure in polymer as a trial, or demonstration, to study how well the new product would fare in this salty environment. “This became Armtec’s first installation of a polymer laminate plate structure in Canada,” says Lowry.
Installation Options
Regardless of the installation method chosen, the new structure was going to be a very tight fit – at some points, a mere 500 mm clearance; so, two installation options were considered: I) build the new structure in sections, outside of the existing one, and progressively slide the assembled structure into the opening; or II) erect the new structure in place, inside the existing one.
“The erection subcontractor, Elliott Underground, opted to erect in situ,” explains Lowry. “The rings of the new arch ring were comprised of five individual 6.0 mm thick plates, so that presented some alignment challenges during installation, as the crew, working in tight quarters, had to maneuver plates into place and ensure all were properly aligned, bolted and torqued. Even so, the installation was completed in the dead of winter, without having to close any lanes of traffic above,” adds Lowry.
As the replacement structure was longer than the original, there was room for some conventional backfill operations which, on the lower portion of the arch, Aecon chose to limit to the four corners/ends. This effectively created four soil dams, which served to retain the un-shrinkable fill (U-fill), up to a height of approximately 1.5 metres above the footing.
U-fill was used where conventional backfill operations would not work due to space constraints. Above the U-fill, conventional backfill procedures were used until there was no longer enough headroom, at which point the general contractor employed conventional roadway protection to facilitate the multiple lane shifts required to avoid road closures. These lane shifts allowed the upper portion of the existing Cast in Place structure to be partially demolished, in stages, and the backfilling and paving operations to be completed sequentially.
“As this was among the first Canadian installations of polymer coated plate, it was an important stepping stone in evaluating, understanding and improving the coating system,” says Lowry. “The lessons learned on this project contributed to development of the much improved Polymer Coated product we produce today.”
“At that time, the first iterations of polymer coated CSP and SPCSP were manufactured by applying polymer over galvanized (zinc) steel,” explains Dave Penny, CSPI Executive Director. “This polymer coating was applied at one end only, where we suspected salt was percolating down from above. And, although it’s holding up very nicely and it still looks great, we learned a number of important things from this demonstration. In fact, the Polymer Coating System for SPCSP is now applied quite differently, and is much better as a result, so the demonstration contributed significantly to improving the quality of the product.”
During this demonstration, some evidence of problems with the coating used on this first generation polymer treatment was observed. As a result of imperfect bonding between the polymer and zinc layer, the coating scratched a bit too easily.
“The initial methodology applied a polymer coating to galvanized steel, which we soon learned had some performance issues, ”explains Lowry, “so we began experimenting with different combinations and permutations, until we arrived at a new and much better way to apply the polymer coating to the steel. We abandoned the use of galvanized steel as a base for the polymer coating, and the entire manufacturing process was revised and improved. The new manufacturing process involves application of a zinc-rich epoxy to white steel (sandblasted black steel), followed by application of the polymer top coat. This new procedure greatly improves adhesion which in turn improves the performance of the coating,” concludes Lowry.
“During the eight years since this Kingston installation, many infrastructure owners have come to accept and trust polymer coated pipe or plate as being a prudent investment in a premium product that delivers longer life and better value in harsh environments that threaten even galvanized steel,” says Penny. “And, since it remains a premium product, customers will now often elect to specify polymer coating only on the part(s) of a structure exposed to the highest risk of corrosion,” he adds. “This demonstration/evaluation is an example of just one of many ways we study performance in the field to learn what needs to change, if we are to continue to improve and expand CSP products and their variants to protect structures from specific environmental threats,” concludes Penny.