To complete the CSP rehabilitation project for twin culverts at Big Slough on behalf of The Corporation of Delta, PW Trenchless, of Surrey, B.C. opted to slip line each structure one at a time, thus eliminating the need to close the road which would inconvenience the people who depend on it every day.
Of course we know corrugated steel pipe (CSP) isn’t the best solution for every soil and water management problem. But we also know that very often it is the best solution. And, if we don’t promote increased awareness of the benefits of steel among customers and prospects, they may not recognize those opportunities when steel clearly represents the best value solution for their water management projects.
This is the first in a series of technical articles intended to share real-life cases that demonstrate the technological advances, specialized coatings and improved installation methods that have been made CSP a leading contender in solving a wider range of project demands than ever before.
In 2011, The Corporation of Delta, the municipal government representing Ladner, North Delta and Tsawwassen, B.C., opted to use an advanced “trenchless” construction process to successfully rehabilitate a pair of twin culverts at Big Slough, situated in an environmentally sensitive area, without having to close Hornby Road, the region’s sole access road for local traffic.
The contract was awarded to PW Trenchless Construction, an experienced, Surrey-based contractor specializing in the rehabilitation of aging infrastructure, through a design build bidding system. The existing twin culverts had deteriorated prematurely as a result of the area’s brackish water. Accordingly, in order to meet the customer’s new requirement for a 75-year service life, PW opted to slip line the existing twin culverts using polymer coated structural plate corrugated steel pipe (PCSPCSP). The co-polymer coating is especially resistant to the aggressive water chemistry at the site.
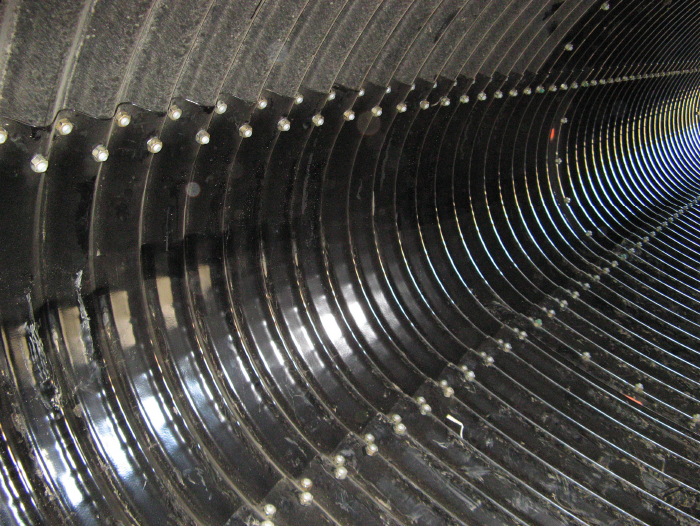
To meet the specified 75-year service life, PW Trenchless used Polymer Coated Structural Plate Corrugated Steel Pipe (SPCSP), which offers maximum protection against specific corrosive threats posed by the aggressive water chemistry of the site.
Polymer coating, as described in CSA Standard G 401, provides two layers of protection; the zinc rich base coat offers outstanding corrosion resistance while the top coat of ethylene acrylic acid (EAA) provides excellent corrosion resistance against diluted acids, salts and alkalis.
For those unfamiliar with trenchless technology, it is a progressive civil engineering approach for installation, replacement and renewal of underground utilities. It greatly minimizes or eliminates excavation and surface disruption, dramatically reducing inconvenience to vehicular and pedestrian traffic, business and residential activities, as well as virtually eliminating the invasiveness of construction practices in environmentally sensitive areas.
Moreover, recent advancements in robotics have enabled trenchless technologies to provide pipe condition diagnostics previously unavailable, permitting utility owners to more accurately identify infrastructure priorities.
“We’ve done quite a few similar relines with SPCSP,” says David O’Sullivan, President of P.W. Trenchless Construction, “so we know it’s a very cost-effective and prudent alternative to the conventional replacement of culverts. Plus, the slip lining methodology eliminates the enormous expense and inconvenience of having to close the road to traffic throughout construction, while providing an inherently safer site than traditional, open trench installations, so it really is a win-win solution,” he adds.
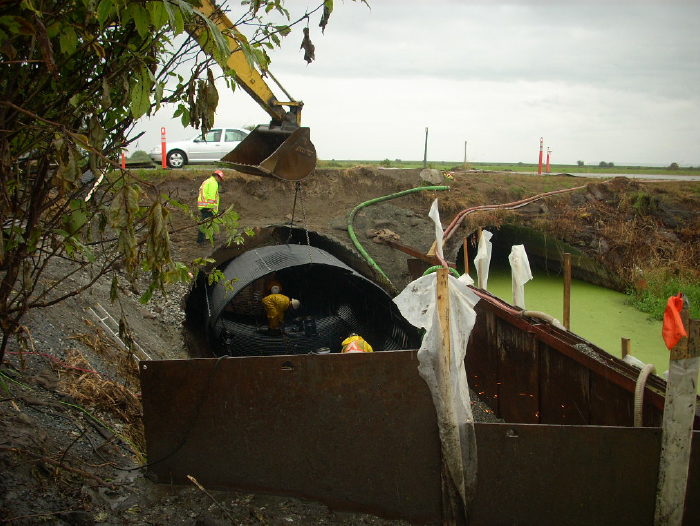
After dewatering, the first assembled SPCSP slipline is being inserted into the original steel plate structure at Big Slough.
Avoiding road closure was accomplished by dewatering one culvert while diverting the entire hydraulic flow to the other structure. As Brock Nesbit, Armtec drainage solutions Sales Supervisor for Western Canada, explains, “After dewatering the first culvert, two rails were affixed to the invert and the new Strata-CAT polymer coated SPCSP pipe arch structure was assembled at the inlet and pushed along the rails into the old structure.”
The annulus was then filled with a low density, non-shrinking cementitious grout, completing rehabilitation of the first culvert. Water flow was then reintroduced to the first structure and the whole process was repeated on the second.
“In addition to avoiding interruption to automotive and pedestrian traffic above, the process also allowed the unobstructed passage of fish and other wildlife below throughout the duration of construction,” says Nesbit.
David Penny, Executive Director of the Corrugated Steel Pipe Institute adds, “The advanced, two-coat co-polymer coating used at Big Slough provides two layers of protection that meets or exceeds industry standards for a 75-year design service life. And it provides ideal protection in environments with a pH range of 3 to 12 and resistivity between 100 to 100000 Ohm-cm,” he says.
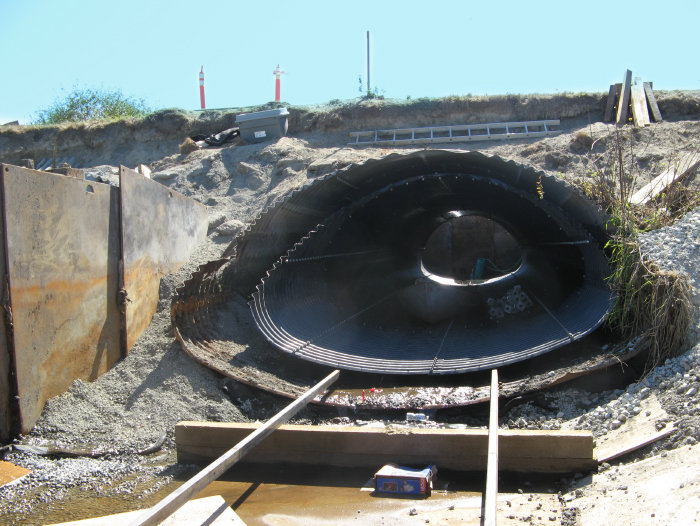
After dewatering the first culvert, two rails were affixed to the invert and the new polymer coated SPCSP pipe arch structure was assembled at the inlet and pushed along the rails into the old structure.
Once the new structure is in place, the annulus was filled with a low density, non-shrinking, cementitious grout, completing rehabilitation of the first culvert. Water flow was then reintroduced to this culvert and the process was repeated for the twin structure.
“This copolymer coating is just one of many application/environment specific CSP coatings developed over the past century to increase longevity and performance by protecting the pipe from specific threats in hostile water chemistry, such as anomalous pH levels, elevated salinity and other specific threats” adds Penny, “and those who think CSP is the same as it was – even just ten years ago – owe it to themselves and their customers to check out just how significantly these new technologies and options have enhanced the versatility, performance and durability of specially coated variants of CSP.”
There’s no doubt CSP sliplining will save considerable time on rehabilitation projects, as it can be installed much faster than replacing a structure – completions are measured in days or weeks, not months – without sacrificing anything in performance. But performance/endurance and uninterrupted passage only describe part of the win/win nature of CSP relines.
There is also a tremendous economic advantage when opting for a slip line. “It’s much cheaper to reline than build a new bridge or culvert, especially when it involves inconveniencing taxpaying stakeholders with detours,” says Penny, “and as anyone working in the public infrastructure segment already knows, budgets are virtually always insufficient to handle the myriad of project demands by the owner. So cost reductions are of paramount importance to all stakeholders, especially to contractors looking to win new bids.”
According to O’Sullivan, “when working with the typical soil and water conditions in this area, choosing whether to spend $10 million for a replacement bridge vs. $400 thousand for a reline is pretty much a financial slam-dunk. Plus, we’re seeing a new trend in cities and DOTs across Canada toward establishing culvert asset management contracts, which include a technical evaluation of the condition of your current infrastructure assets, and a planned/managed regimen for their timely inspection, rehabilitation, or replacement.”
As well as offering huge cost savings, enhanced durability and faster, non-invasive installation, the fourth principal benefit is that this CSP reline technique is also ’greener’ than conventional rehabilitation methodologies. First, the steel used in manufacturing CSP is totally recyclable and already contains more than 51% recycled steel.
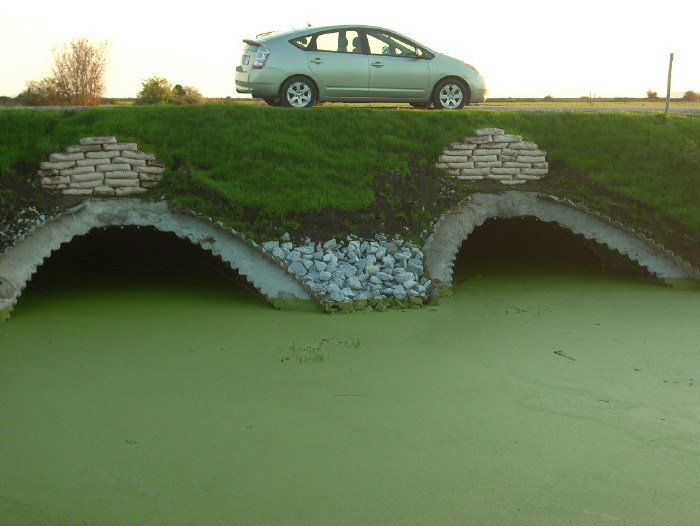
The finished polymer coated SPCSP reline was completed and operational in about two weeks, with virtually no interruption to the citizens and businesses operating in the bustling Delta area of B.C.
“The significant reduction of a project’s environmental impact is already extremely important to conserving our finite resources,” says Penny, “but, in future it will also become an increasingly important financial criterion for those involved in construction and maintenance of infrastructure projects, as well,” he continues. “And that is because the current voluntary guidelines targeting carbon neutrality will inevitably evolve into a quantifiable, monetized component of infrastructure project costs. And, when that happens, failure to adhere to the new environmental protocols will add significantly to construction costs for anyone who fails to comply,” he concludes.
To make it easier to calculate the environmental impacts of replacing a culvert using trenchless vs. open cut construction methods and compare the resultant carbon footprints, PW Trenchless, with funding from the Government of Canada and in collaboration with the B.C. chapter of the North American Society for Trenchless Technology (NASTT), has developed a practical Carbon Calculator, available at http://utilitycarboncalculator.com
Additionally, carbon emissions from manufacturing, transporting and installing SPCSP structures are all significantly reduced versus using alternative materials and techniques. Steel plates are manufactured and coated offsite in a controlled factory environment. Similarly, because the steel plates are relatively lightweight and can be nested in a compact load, significantly less carbon is produced in transporting components to the job site. And, lastly, because no heavy machinery is required for reline installation, onsite carbon emissions are also appreciably reduced.
“When you opt to do a reline, you’re not just saving money, you’re also eliminating the need to draw in valuable resources to the site,” adds Penny, “which would have added considerably to carbon emissions at the construction site, on haul roads and borrow pits – something that is especially important when working in a bog, which was the case at Big Slough.”
To find out more about relining pipe arches and large pipe for rehabilitation projects, please refer to the detailed Technical Bulletin 7 available on CSPI website at:
http://www.cspi.ca/sites/default/files/download/cspiTECSeven_103.pdf -